The process of manufacturing glass bottle
2015-03-13
Raw Materials
There are four main ingredients used to manufacture glass: Silica sand, soda ash, limestone and recycled glass (cullet).
There are also a variety of minor ingredients, (some are included to give glass its color). These raw materials are simple and readily available.
The process used today is more sophisticated and highly technical.
The materials are stored in the Batch House in compartments, gravity fed into the weighing and mixing area, and finally elevated into batch hoppers, which supply the glass furnaces.
Furnace
The two furnaces are capable of producing 30 tonnes of glass per day.
Firing is by natural gas through the side ports and the glass temperature in the furnace ranges from about 1590 degrees Celsius.
Molten glass flows out through two feeders to the forming machines attached to each furnace.
Economical melting [within the furnace] of raw materials into glass requires constant supervision and monitoring with the use of sophisticated computer-based control systems.
From the furnace, the melted glass goes to the refiner and then the forehearth where the glass is cut before entering a bottle forming machine. These are either double or triple gob machines.
The numbers of gob vary depending on how many sections are in the forming machines. The sections within the forming machine contain bottle or jar moulds. Each mould comprises 11 separate pieces and a large forming machine can carry as many as 30 moulds.
Anneal
Anneal is to toughen (glass or metals) by heating and slow cooling.
An annealing lehr is a long, flat oven, which first reheats the bottles to 550 degrees Celsius and then gradually cools them until they emerge at the cold end, between 30 minutes and one hour later.
Annealing is necessary because the glass is a poor conductor of heat and cools unevenly when it emerges from the forming machine.
The lehr ensures even cooling of the whole bottle, which reduces residual stresses inside the glass.
The bottles are given two surface treatments during their journey through the lehr. One at the end which helps maintain their strength, and one at the old end which helps prevent scratching.
The surface treatments also aid bottles to move smoothly along the filling line at a customer plant.
After leaving the cold end of the lehr, bottles then pass through electronic inspection machines, which automatically detect faults.
These include, wall thickness inspection, squeeze testing, sealing surface inspection, side wall scanning and base scanning.
The information from the quality inspection machines is relayed back to the end? Forming machine operators who can then make adjustments to remove the problem.
Rejected bottles are returned to the raw materials area and recycled as cullet in the batch for making new glass.
Quality inspection is an essential part of the manufacturing process. It ensures the best product possible is always distributed to customers.
Distribution / Customer
Once the bottles have passed inspection, they are packed in pallets.
Each pallet can be 4-11 layers high and contain as many as 5000 bottles. Once the pallet has been assembled, a large plastic envelope is placed over it and shrunk until tight. This makes sure the pallet is stable, ready for transportation to the warehouse.
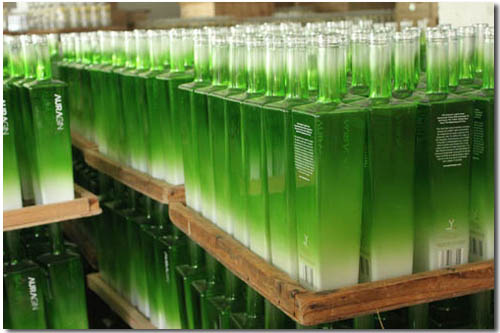
There are four main ingredients used to manufacture glass: Silica sand, soda ash, limestone and recycled glass (cullet).
There are also a variety of minor ingredients, (some are included to give glass its color). These raw materials are simple and readily available.
The process used today is more sophisticated and highly technical.
The materials are stored in the Batch House in compartments, gravity fed into the weighing and mixing area, and finally elevated into batch hoppers, which supply the glass furnaces.
Furnace
The two furnaces are capable of producing 30 tonnes of glass per day.
Firing is by natural gas through the side ports and the glass temperature in the furnace ranges from about 1590 degrees Celsius.
Molten glass flows out through two feeders to the forming machines attached to each furnace.
Economical melting [within the furnace] of raw materials into glass requires constant supervision and monitoring with the use of sophisticated computer-based control systems.
From the furnace, the melted glass goes to the refiner and then the forehearth where the glass is cut before entering a bottle forming machine. These are either double or triple gob machines.
The numbers of gob vary depending on how many sections are in the forming machines. The sections within the forming machine contain bottle or jar moulds. Each mould comprises 11 separate pieces and a large forming machine can carry as many as 30 moulds.
Anneal
Anneal is to toughen (glass or metals) by heating and slow cooling.
An annealing lehr is a long, flat oven, which first reheats the bottles to 550 degrees Celsius and then gradually cools them until they emerge at the cold end, between 30 minutes and one hour later.
Annealing is necessary because the glass is a poor conductor of heat and cools unevenly when it emerges from the forming machine.
The lehr ensures even cooling of the whole bottle, which reduces residual stresses inside the glass.
The bottles are given two surface treatments during their journey through the lehr. One at the end which helps maintain their strength, and one at the old end which helps prevent scratching.
The surface treatments also aid bottles to move smoothly along the filling line at a customer plant.
After leaving the cold end of the lehr, bottles then pass through electronic inspection machines, which automatically detect faults.
These include, wall thickness inspection, squeeze testing, sealing surface inspection, side wall scanning and base scanning.
The information from the quality inspection machines is relayed back to the end? Forming machine operators who can then make adjustments to remove the problem.
Rejected bottles are returned to the raw materials area and recycled as cullet in the batch for making new glass.
Quality inspection is an essential part of the manufacturing process. It ensures the best product possible is always distributed to customers.
Distribution / Customer
Once the bottles have passed inspection, they are packed in pallets.
Each pallet can be 4-11 layers high and contain as many as 5000 bottles. Once the pallet has been assembled, a large plastic envelope is placed over it and shrunk until tight. This makes sure the pallet is stable, ready for transportation to the warehouse.
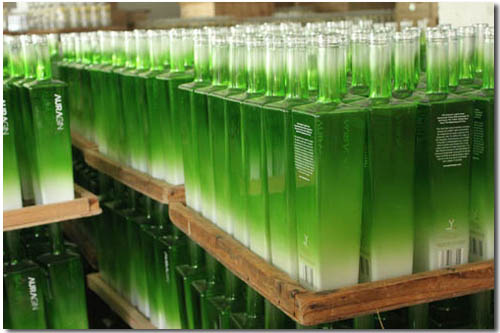